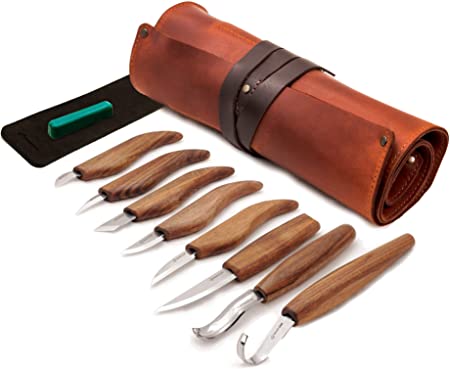
If chip carving has ever been something you've wanted to do, you know how difficult it can be. There are many styles and techniques you can use, but which one is the best? What tools do you need? Here are my tips and tricks to carve chips. I hope this helps you decide what one is best for you. You can carve potato chips in a traditional or more modern way, but there are some essentials that will help you succeed.
Traditional
Chip carving can be considered one of the oldest forms in decorative woodcarving. A straight-edged knife is required, however, a skew ground or offset blade knife may also be used. Chip carving is the process of making small triangular incisions on wood to create a pattern. This art form developed over 1,000 years ago. It has been adapted in many other countries. Because of its widespread popularity, the designs were often so similar across nationalities that it was impossible to discern one from another.
As the practice spread throughout the world, the skills required to carve wood were passed down from generation to generation. Chip carving was an art form used to decorate furniture in Sweden. Schools were created to teach the art. The skills and knowledge of carvers from centuries ago have benefited modern chip carvers. Through the generations, knowledge was passed from carver to apprentice to student. It is a long-lasting process that continues today.
Free Form
If you've always wanted to try chip carving, you've come to the right place. Murray Taylor's DVD shows you how to make freeform and geometric carvings. This DVD is a great introductory project that provides lots of information. English and NTSC formats can be found. The DVD is also available in widescreen and stereo. Artisan Media Ltd. owns the DVD and it's available in MP4 for Windows and Mac computers.

Triangles, circles and lines are the basic shapes of geometric chip carving. This technique is flexible and can be used in a variety of styles. This method of chip carving is also called freeform chip carving. Regardless of whether you want your chips to be a flower or a dragon, it will be a wonderful addition to any room. You can incorporate multiple techniques into one piece by free-form chip carving.
Techniques
Chip carving has been practiced for hundreds of years. There are many examples all over the world. You can find chip carving on boats paddles and other ceremonial tools handles in the South Pacific Islands. These carvings were most likely done using bits of bone and sea shells, but some people have reported using shark teeth as well. This book will show you how to create amazing designs by using different chip carving techniques.
If you are able to follow some simple steps, chip carving can be easy. First, you need to learn how to carve the fine triangular shape. This pattern is easy to understand and easy to execute. Simply carve several triangles and continue this process until you have carved the pattern. It doesn't have to be boring. Simply by changing the angles, you can create amazing patterns.
Tools
You can learn the basic steps of chip carving by attending a free online seminar from Lora S. Irish. She will show you how to use various carving tools, including a stab knife, chip knife, and detail bench knife. Irish will also cover the various types of wood carving tools in this free seminar. The list below will help you choose the right tool to suit your carving needs. These tools are versatile enough to create simple shapes or intricate designs.
A chip carving knife uses special geometry. It is approximately 1 1/2 inches long with a narrow back edge. This allows for precise incisions. Also, it is important to pick a sharp point for the needle so that the edges meet perfectly. The chip carving knives are made from stainless steel with a sharp tip. A chip carving knife should be sharp and sharp enough to slice a bit of wood.
Getting started
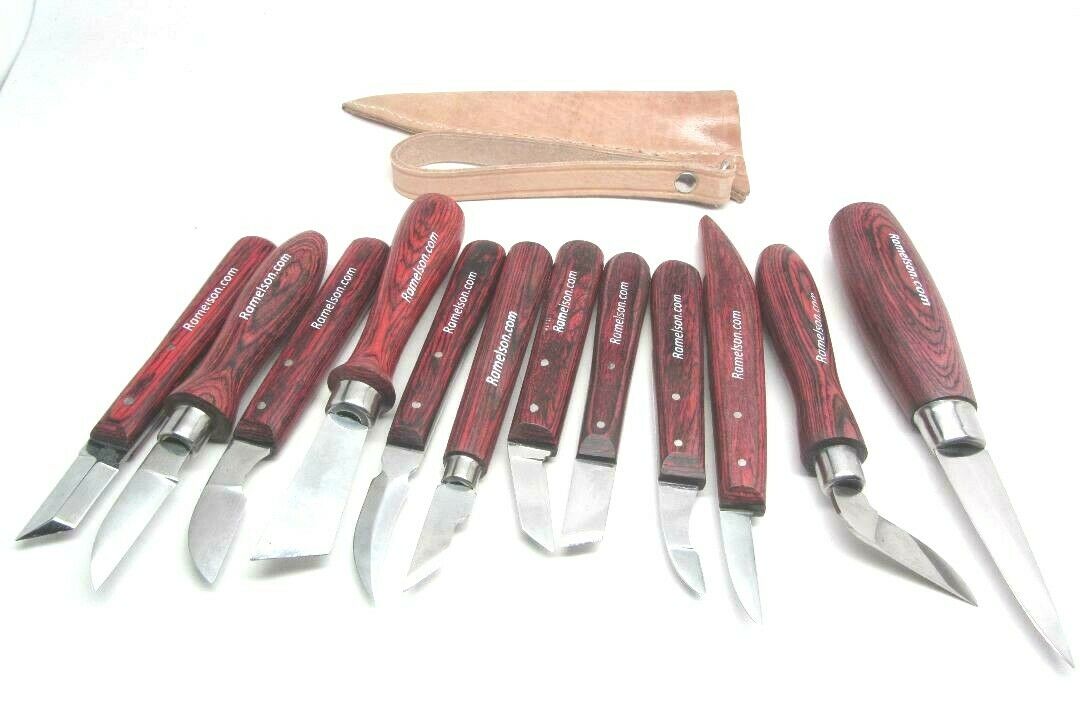
When getting started with chip carving, you must first learn about its methodology. The method you choose will depend on the type and purpose of your carving. However, these principles will help you ensure your work is accurate. The chip carving method involves making a pattern in the wood. Follow these steps for your first chip carving:
Sharpening a chip carving blade is crucial. Chip carving knives will have bevels along their blades, which indicates they are primary chip carving knives. The sharpening tool is shaped like a small diamond and can produce sharp edges. Place it at a ten degree angle. The stone will sharpen the chip carving knife and chip carving tool at the same time.
FAQ
How do you know which type of wood you are working with?
Always check the label before purchasing wood. The label should contain information about the wood species, its moisture content, and whether it has been treated with preservatives.
What would be your first step in woodworking?
Start with softwoods, such as pine or poplar. After you are comfortable with the softwoods, move to hardwood.
Do you have any other information I should know about woodworking and/or the process of making it?
Furniture making is a laborious task. It's easy not to appreciate how hard it is. Finding the right kind of wood is the most difficult part. It is difficult to choose between the various types of wood.
Another problem is that not all wood has uniform properties. Woods can warp, split, or crack over time. Before purchasing wood, you should consider these factors.
Statistics
- Average lumber prices rose about 600 percent between April 2020 and May 2021. (familyhandyman.com)
- Woodworkers on the lower end of that spectrum, the bottom 10% to be exact, make roughly $24,000 a year, while the top 10% makes $108,000. (zippia.com)
- The best-paid 10 percent make $76,000, while the lowest-paid 10 percent make $34,000. (zippia.com)
- In 2014, there were just over 237,000 jobs for all woodworkers, with other wood product manufacturing employing 23 percent; wood kitchen cabinets and countertop manufacturing employing 21 percent. (theartcareerproject.com)
External Links
How To
How to join wood without using nails
Woodworking is an enjoyable hobby. It is relaxing and enjoyable because you can create something useful with wood. Sometimes you may want to join two pieces together of wood without using nails. This article will explain how to do this so that your woodwork projects stay beautiful.
Before joining the pieces of wood together, you will need to first trim any edges. You don't want to leave sharp corners that could cause problems later on down the road. After you have completed this step, you are ready to glue your boards together.
If you're working with hardwood, you should only apply glue to one side. For softwoods like cedar and pine, glue should be applied to both sides. Once you have applied the glue, press down on the boards until they are fully attached. After applying the glue, let dry the boards before proceeding to the next stage.
After you have glued the boards together, drill holes in the joints where you intend to place screws. The size of these holes depends on what type of screw you choose to use. For example, if you're going to use a 1/2-inch wood screw, then you should drill a hole that is at least 3/4 inches deep.
Once you have drilled your holes you will need to drive the screws through each joint and into the backside. Do not hit the boards' front surfaces. It will ruin the finish. Try to not hit the ends of the screws when driving the screws. This will avoid splitting in the wood's ends grain.
Protect your finished project now. To do this, you can seal the entire furniture piece or just cover the top. You want it to last years, so you can use any product. Some examples include oil-based varnishes, polyurethane, shellac, lacquer, etc.
You can find these products at most home improvement stores. Just make sure that you buy the right kind for the job. Some finishes are toxic and should not ever be used indoors. Protective gear should always be worn when handling these finishes.