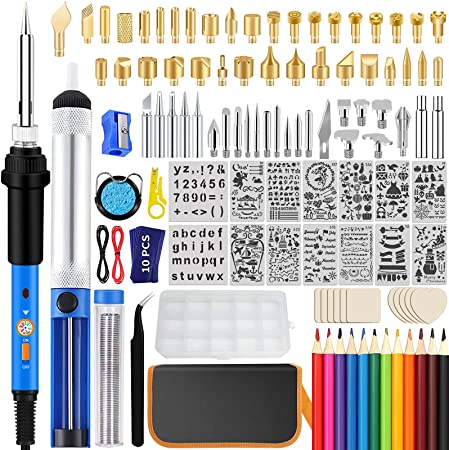
You will need to draw your desired design in order to make a wood burning cutter board. It doesn't matter if your drawing is simple or complicated. You have two options: you can transfer the drawing onto a cutting board using transfer paper, or you can cover it with graphite and trace the outline with lots of pressure. Then heat up the wood burning tool. The proper tip size is important. You can use one that is small or one that is thicker, depending on the detail you need.
Mineral oil
Mineral oil can be used to enhance the design of your cutting board. This natural oil will repel water, keeping the wood from absorbing any liquids. There are many forms of mineral oil. It is inert, non-toxic and can be stored for up to six months. Mineral oil can be used safely for human consumption. You can use it once or twice per month, or whenever the cutting board starts to dry.
Food-grade mineral oil is the safest option. The product is refined past other oils, so it's considered food-safe. To find out more, please refer to the label. There are many good options, such as Howard's Cutting Board Oil (Food-Grade Mineral Oil) and Howard's Cutting Board Oil (Food-Grade Mineral Oil). Check the label carefully to make sure you are safe from mineral oil. If your board doesn't have a label, consider other options such beeswax.
Walnut oil
Consider the type of finish you prefer when choosing walnut oil wood burning cutting boards. Mineral oil is a good choice, as it is non-toxic and fills in the wood's pores without actually penetrating the wood's surface. Walnut oil is also a good choice because it repels food and water. Walnut oil comes from walnuts and is water-repellent. It takes a while to dry.
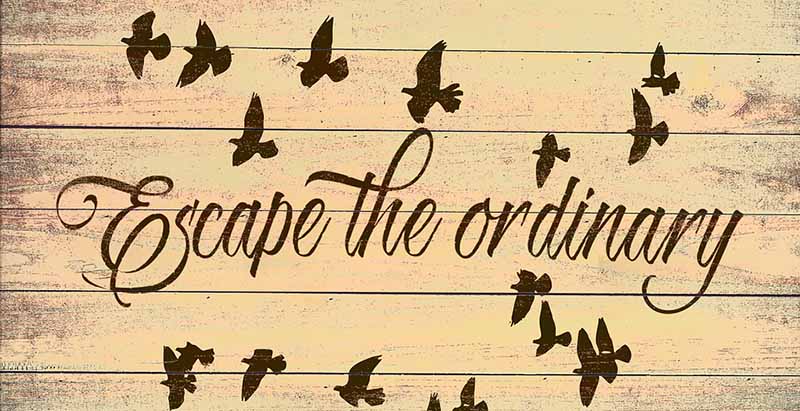
It's important to remember that walnut oil is not similar to mineral oil, which is sourced from petroleum. Walnut oil is derived from the humble Walnut tree. Although you might be tempted to use cooking-grade walnut oils on your cutting boards. However, the oil will quickly become rancid so it is better to use heat-treated and filtered Walnut oil. You'll be in a position to preserve the board's condition over many years.
Linseed oil
A variety of oils can be used to make a wood burning cutting table. Walnut oil, mineral oil and beeswax are often used to seal wood. Walnut oil is great for cutting boards because it is slow drying, repels water and keeps bacteria away. It is also not toxic.
Make sure you choose a high-quality brand when choosing linseed oils for your project. It should be non-toxic, and safe for kids. Raw linseed is completely free from preservatives and additives. Each coat will take at least three to four days to fully dry. It is best to dilute the product with an odorless solvent or citrus solvent before you apply it to barewood.
Beeswax
You can make wooden cutting boards with beeswax. The natural oil fills the pores of the wood. This mixture repels liquids and is water-resistant. Beeswax also works well for conditioning wood products. To finish your cutting boards, you can either use mineral oil or mix beeswax and mineral oil. Apply the mixture evenly to the surface of the board and let it dry for a few hours. Polish the board to give it an durable shine.
A spoon or a board butter can be used to apply the wax. When waxing wood, it's important to keep it warm. To avoid the wood from setting immediately, use a hairdryer or heat gun to pre-heat it first. Apply the wax section by section to the board. It is important to remember that the wax will cool quickly. Before applying wax, dip a toothbrush in the wax.
Tung oil
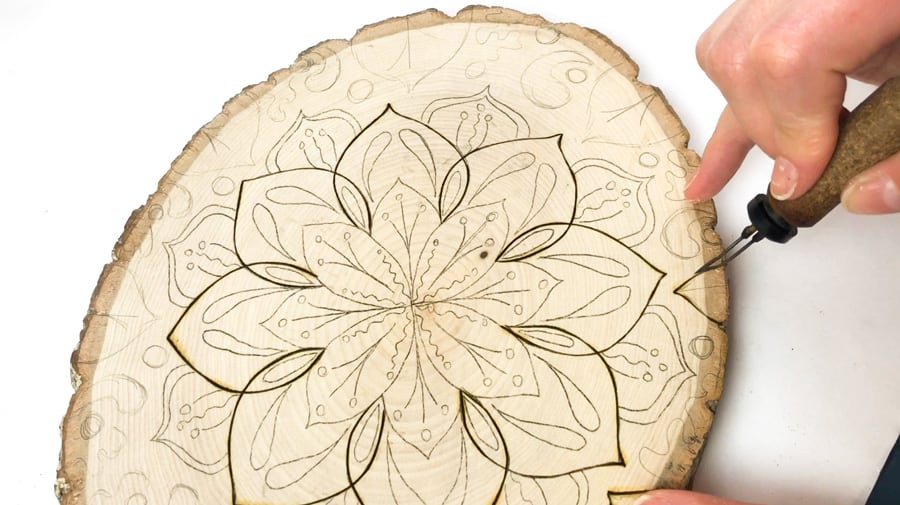
You can use tung oils to make a wood burning cuttingboard. Tung oil comes from the seeds and nuts of tung trees. It hardens once applied and gives the cutting boards a shiny, dry finish. Non-toxic and with a deep penetration into the wood, tung oils is an excellent choice for sealing. Tung oil can be used in kitchens to dry the wood quickly and also prevents water from entering the board.
This process requires the use of Pure Tung Oil, which is available at any home improvement store. If this product is used properly, it can last for years. Just apply a generous amount to your surface and let it dry completely. You can then apply tung oils to your board. You should apply a layer of oil to a new wood cutting board. You might want to repeat the process if your cutting board is not durable enough to withstand the use of knives or other kitchenware.
FAQ
What is the minimum investment a hobbyist needs to make in order to get started?
You will need capital to purchase the tools and supplies you need to start your woodworking business. It's a good idea to buy a small tablesaw, drill press and circular saw. These items aren’t too expensive so you won’t have to break the bank.
What kind of tools do carpenters use?
A hammer is probably the most widely used tool for carpenters. A hammer is used for pounding nails into wood. It is also used to help hold pieces together while working on a job. Other tools include clamps.
How can I keep my shop organized?
The first step toward keeping your workshop clean and organized is to set aside a designated area for storing tools. Keep your tools away from dust and debris, so they stay sharp and ready to work. You can hang tools and accessories with pegboard hooks.
Statistics
- In 2014, there were just over 237,000 jobs for all woodworkers, with other wood product manufacturing employing 23 percent; wood kitchen cabinets and countertop manufacturing employing 21 percent. (theartcareerproject.com)
- The U.S. Bureau of Labor Statistics (BLS) estimates that the number of jobs for woodworkers will decline by 4% between 2019 and 2029. (indeed.com)
- Most woodworkers agree that lumber moisture needs to be under 10% for building furniture. (woodandshop.com)
- The best-paid 10 percent make $76,000, while the lowest-paid 10 percent make $34,000. (zippia.com)
External Links
How To
How to stain wood
Staining wood can be described as a process where chemicals are applied to the wood surface. This causes the wood to take on a new color. This chemical reaction causes the wood to change from white to brownish red. Oak is the most common wood type for staining. However, you can also use other wood types.
You can apply wood stains in many different ways. One method involves mixing the stain and a solvent and then spraying it on the wood. Another method involves applying a solution of water to the wood. Stains can also be mixed into paints and varnishes, becoming part of the finish coating.
Preparing your wood for staining is the first thing to do. Cleaning the wood thoroughly removes any dirt or grease that could interfere with applying the stain. Sanding the wood smooths out rough spots and scratches. The next step is to determine the type of stain you would like to use. There are two main kinds of stains available: non-penetrating stains and penetrating. Penetrating colors penetrate deeper into wood than those that are non-penetrating. This makes them more suitable for darker colors, such as mahogany. The best non-penetrating colors are those that work with light colors like maple.
After you've decided what type of stain to apply, get ready for your tools. Paintbrushes are great for applying stain because they allow you to evenly spread the liquid across the surface. To remove any stains left behind after painting, you will need some rags. If you intend to mix the stain yourself you will need enough containers to hold all the components.
Once you have prepared all your materials, it is time to clean the areas where you will stain the wood. Clean the area with soap and warm water to get rid of dirt and grime. Wipe down all furniture pieces with a dampened cloth and clean water. If you intend to stain darker wood, make sure you get rid of any debris.
Apply the stain next. The stain can be applied by spraying or brushing the stain onto one end of the furniture. Slowly and carefully work your way along the grain to reach the opposite end. Make sure that the stain does not drip off the edge of the wood. Let the stain dry completely before proceeding with the next steps.
Clear polyurethane is used to protect the painted surfaces. Three coats of polyurethane sealing agent are required. Allow the third coat of polyurethane sealer to dry overnight before applying the final coat.