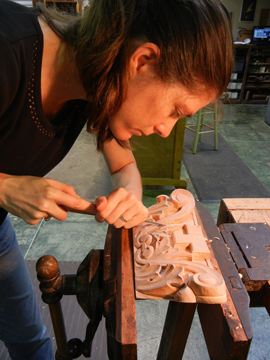
Select a piece of wood to begin carving a face out of wood. Make the necessary cuts. As the expert guides, you can watch a video that shows the entire process step-by-step. The progressing cut will make carving the face much more realistic. The key to creating a lifelike visage is the progression of your noses on the piece of wood. To create a lifelike finish, you can use colored dyes or shellac.
Hardwoods
The type of wood used to carve a face in wood must be considered before you begin carving. Hardwoods are broad-leaved trees that can grow in all climates. They are suitable for many purposes including furniture and building because of their high density, strength and beautiful appearance. Hardwoods can be more expensive, but they are also more durable and resistant to fire.
You might want to try wood carving if you are new to the art. These types of wood are more easy to work and are an excellent choice for beginners. However, you should remember that softer woods cannot hold the same quality and finish as hardwoods. For this reason, it's important to experiment with different types of wood before settling on a particular type.
Softwoods
The first step when carving a face in wood is choosing the softwood to use. Softwoods are more difficult to carve, and often will have many knots. They also tend to break more easily, especially if you make large strokes. The smallest pieces of wood will be cut by a beginner carver, which reduces the amount of detail. While this isn't a major issue, it is something to be aware of.
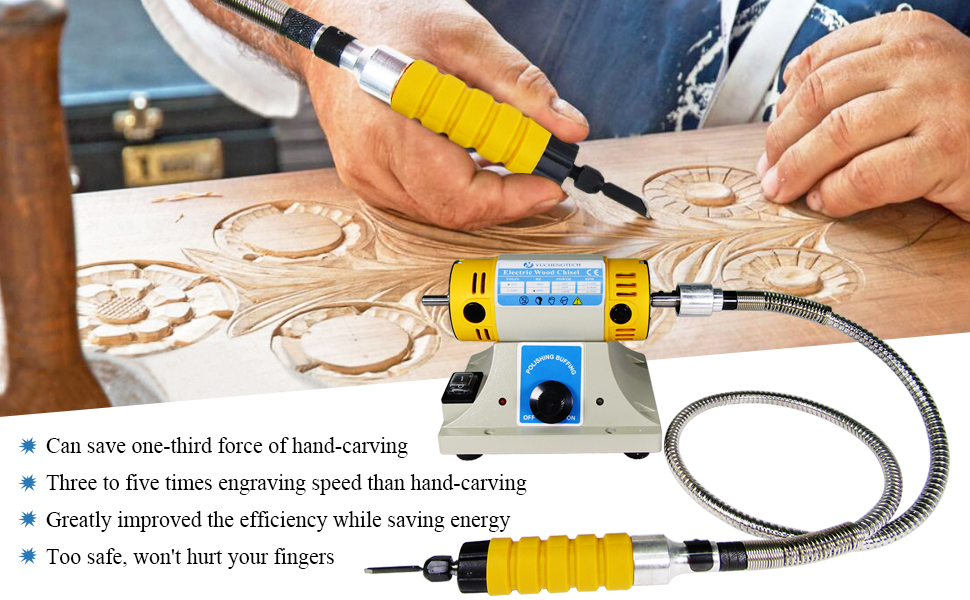
Some hardwoods can be more difficult than others. Aspen and butternut are the easiest hardwoods to work with. A steeper bevel is better for this reason. Softwoods are easier than hardwoods to work with, and can be carved along the grain or across it. The quality of the final product will be determined by the wood used for carving.
Colored dyes
You can create a bright, detailed finish to a wood carving by using colored dyes. These can be found in a variety of colors. You can also mix them with water or alcohol for a unique look. For lighter woods, you can use colored dyes mixed with shellac. To clean the brushes after applying dyes, be sure to ventilate. Another option is paste wax. Be aware that an excessive glossiness may distract from your work. Use 0000 steelwool to get rid of any excess glossiness.
There are many wood dyes available and they can be applied easily. Wood dyes work well with all topcoats. They can solve common finishing problems. They are easy to mix and use because they come in many primary colors. They're also available in a variety of shades and can be mixed according to individual preference. They can be mixed to create new colors.
Shellac
It is important to have the shellac ready before applying it on your wood carving. A jar of shellac is available, but the best way to apply it to your wood carving is with a brush. A two-pound cut is sufficient. This is because it will grow slowly and will reduce the brush marks. A thicker cut is better than a thin one because shellac can be very water-thin. Make a pad from small, golf-ball-sized pieces of cotton and lint-free cloth to ensure you get the correct amount. Then, dip the tip of your brush into the shellac and let the excess flow back into the bottle.
Shellac is used to highlight grain and give it color. Shellac comes with a wide range of colors. You can mix different shades to make your own custom blends. The lac can be used to darken the color. Shellac, unlike other wood finishes won't turn yellow or become cloudy. Shellac is also more durable, which means you can make even more faces. You can do this with almost any type of woodcarving project.
Gouges
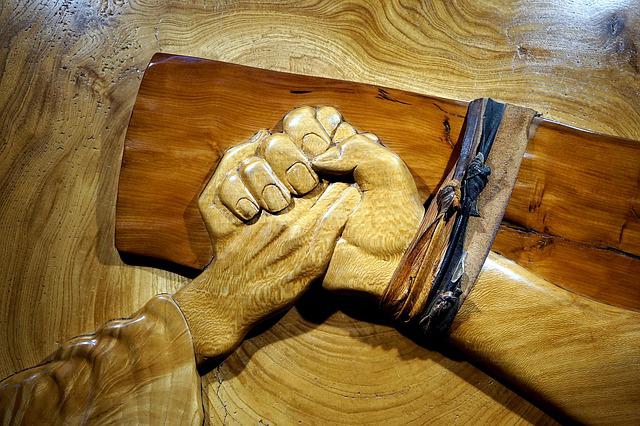
There are many types of gouges. Straight and palm gouges are two of the most popular types. Straight gouges are designed to be held by hand while palm gouges have shorter shafts and handles. Handheld carving is made easier by the shorter handles. These palm gouges can also be called veiners. They are perfect for carving faces into wood. These are some important things to remember before you begin carving.
First, learn how to choose the best gouge. The gouge you choose must be capable of creating a shallow, v-shaped groove. Make sure you buy a tool with a sharp edge and a small sweep. Gouges are commonly classified by size. A 3/10 gouge will create the same-sized cut as an 5/10 gouge. As the first number increases the scoop between edges becomes deeper, and the sweep becomes progressively curvier. A small sweep can carve a shallow profile in a gouge.
FAQ
How does a beginner woodworker earn money?
Many people want to open an online furniture business and are learning how to build it. However, if you're just getting into furniture building, there are other options than selling on Etsy. You can sell at local craft fairs. A workshop could also be offered for people who are interested to learn how they can build their own furniture. You might be able to offer services like remodeling homes or making custom pieces for clients if you are a skilled carpenter.
How often do I need to buy new supplies
You'll probably have to replace some of your tools over time. Hand tools will need to be sharpened regularly. If you are using power tools, you will need to purchase replacement parts regularly. Try spreading your purchases over a few months so you don't buy too many at once.
How do I learn basic woodworking skills?
You can start building furniture by making a bench. This project can be done with any kind of wood that you have at home. If you aren't sure what type of wood to use, you can buy cheap pine boards from Lowes or Home Depot. After you've constructed your bench you'll want sand all the rough edges off and varnish it.
How long does it usually take to complete a piece furniture?
It depends on the type and complexity of your design as well as the amount of finishing that you use. Hardwoods are more difficult to maintain than softwoods. Hardwoods are more expensive than other woods. However, they are stronger and more resistant to moisture. It takes between one and three months to finish a piece.
Where can I locate free woodworking plans
To find free woodworking plans, you don't have to buy any magazines or books. You only need to Google search. You can search Google for "free woodworking" and hundreds of websites will appear allowing you to download plans.
Statistics
- The U.S. Bureau of Labor Statistics (BLS) estimates that the number of jobs for woodworkers will decline by 4% between 2019 and 2029. (indeed.com)
- If your lumber isn't as dry as you would like when you purchase it (over 22% in Glen Huey's opinion…probably over 10-15% in my opinion), then it's a good idea to let it acclimate to your workshop for a couple of weeks. (woodandshop.com)
- Most woodworkers agree that lumber moisture needs to be under 10% for building furniture. (woodandshop.com)
- Woodworkers on the lower end of that spectrum, the bottom 10% to be exact, make roughly $24,000 a year, while the top 10% makes $108,000. (zippia.com)
External Links
How To
How to join wood with no nails
Woodworking is a popular hobby. You can make useful items from wood with your hands, which is both relaxing and fun. You might want to join two pieces from the same wood, but you don't need to use nails. This article will help you to maintain the beauty of your woodwork projects.
First, remove any sharp edges from the wood pieces before you join them. Avoid leaving sharp edges that could lead to problems later. Once you've done this, you're ready to start gluing your boards together.
You should only glue one side of hardwood. If you are using softwoods such pine or cedar, glue should only be applied to one side. Once you have applied the glue, press down on the boards until they are fully attached. Before you proceed to the next step, be sure to let the glue dry completely.
After you have glued your boards, drill holes where you want to insert screws. You can choose the type of screw to determine the size of your holes. If you are going to use a half-inch wood screw, you will need to drill at least 3/4 inch deep.
After drilling the holes, you can drive the screws into your board's backside. Be careful not to hit the front surface of the board, or else you'll ruin the finish. When driving the screws, try to avoid hitting the ends of the screws too much. This will avoid splitting in the wood's ends grain.
Now that your project is finished, you'll want to protect it from the elements. To do this, you can seal the entire furniture piece or just cover the top. You'll want a product that lasts for many years. Some examples include oil-based varnishes, polyurethane, shellac, lacquer, etc.
These products are available at most home improvement stores. You should make sure you are getting the right type for the job. Remember that some finishes can be toxic, so you should not use them indoors. Wear protective gear whenever you are handling them.