
If you are looking to create beautiful and custom pieces for home, you might be interested learning more about pyrography. This ancient art involves burning intricate decorations and designs into wood. It dates back at least to the 17th-century. The resultant burn marks make beautiful dark designs. This can include landscapes as well as portraits. This method is popular for home decor and has been used for centuries.
Yoko sugi ban
The technique of shou sugiban, which is charring wood's surface, was developed in Japan in the 18th century. This gives wood a dark charcoal-black color and can give it a cracked or alligator skin appearance. Japanese cedar is a popular choice for a rustic, traditional look. Other wood species are possible with varying degrees. The wood will be protected from future damage through controlled charring. This is an excellent preservation technique.
Shau sugi ban
The only difference between shou, sugi ban sanding and traditional sanding lies in the way that char is removed. Shau sugiban woodworkers use wire brushes to remove the charred surface, while others use coarse or coarse sandpaper. Either way, you want to scrape away enough char to reveal the brownish black color beneath. The result will look like an alligator's skin, so sanding is essential to remove any excess char.
Shau sugi ban on cedar
While shou sugi ban on pyrography creates an appealing wood finish, it has practical implications. People can inhale bits of charred timber and track them throughout buildings. In order to address this issue, pyrographers now use a propane torch as an alternative to traditional wood-burning. Here is a look at the differences between the two styles.
Yakisugi ban on bassewood
Yokisugi ban on cedar, a centuries-old Japanese method, can increase wood's beauty as well as its durability. Although sometimes called Shou-sugi ban, the process involves charring wood to create beautiful patterns. This technique is so popular in Japan, that cedar is used to make many shousugi ban projects. Satoshi Kimura is the operations director at a Japanese woodworking firm. He explains why shou-sugi ban is so beloved and what it means for woodworkers.
Yakisugi bans blue stain pine
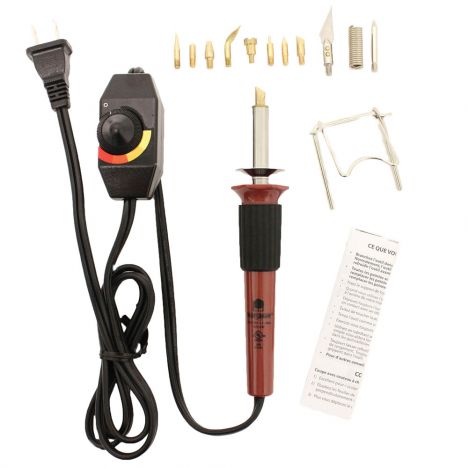
This is commonly known as shou-sugi ban. It preserves wood using fire. Traditionally, cedar is used for shou sugi ban, but other types of wood are also suitable. Although cedar has been used traditionally for this process however, yakisugi is also possible with other woods, such as maple, Ash, and Birch. This technique is popular among traditional Japanese craftspeople.
Shau sugi ban on basswood
Charring cedar pieces gives them a deep, rich black color and a unique crackled surface. Cedar is naturally water-resistant and repels pests. However, the charred surface has sculpting qualities. There are two options for charred wood: untreated or reclaimed. Another option is to treat a cedar board to get a subtler burnt finish.
Shau sugi ban on jelutong
Shou sugi bans pyrography on wood. For starters, the technique enhances the natural patterns of wood. A thicker carbon coating makes charred wood stronger and more long-lasting. This is largely dependent on the timber species and the environment in which it is applied. Shou sugi ban is a great option if you are looking for an environmentally-friendly way to treat wood.
FAQ
Do I have the potential to make a decent living doing this?
Yes! In fact, many woodworkers already do. According to the U.S. Bureau of Labor Statistics in May 2012, the median annual income for woodworkers was $34,000 This is more than the national average of 31,000 per annum.
How long does it usually take to complete a piece furniture?
It all depends on what type of wood you use, how complex your design is, and how much finishing you use. Hardwoods are more difficult to maintain than softwoods. Hardwoods are also more expensive than softwoods. They last longer and are more resistant to moisture. The average time it takes to finish furniture is one week to three weeks.
How much money do you need to get going?
Because every project is unique, there aren't exact numbers. But if you want to get an idea of how much money you'll need, consider these factors:
-
Material cost
-
Tools and equipment
-
The time spent on the project
-
Hourly rate
-
How much profit do you expect to earn
-
You can hire help, regardless of whether you have a plan.
If you're just starting out, you may decide to start small by making simple items such as boxes and picture frames. As you gain more experience, you will be able tackle more complicated projects.
What is the difference between a hobbyist or a professional woodworker, and how can you tell?
Hobbyists like making things with wood. Professionals focus more on quality. Hobbyists tend to take pride and share their creations with family and friends. Professionals spend hours researching design ideas before starting to work on a project. They will meticulously plan every detail of their work from choosing the right materials to finishing it.
Is it easy to start a woodworking business?
It's not easy to start your own woodworking business. There are many requirements and regulations that must be followed. You don't have to go through all that hassle of setting it up. Many people opt to join existing businesses instead. This will allow you to avoid paying membership fees and taxes.
What kind tools do carpenters use to build?
Carpenters use a hammer as their most common tool. The hammer is used to pound nails into wood. It is also used to help hold pieces together while working on a job. Other tools include clamps. pliers. screwdrivers. measuring tape. pencils. saws. drills. wrenches.
Do you have any advice on how to start a woodworking business.
It takes a lot of effort to start a woodworking business. You won't mind working hard if your hobby is something you love. You'll likely enjoy the challenge of owning your business.
When you are launching a new venture, it is important to be aware of the possibility that you will encounter unexpected difficulties. For instance, you might run out of money unexpectedly. Maybe customers won't be willing to pay what you want. You need to be ready for these situations if you want to survive.
One tip is to have a separate banking account for your company. You'll be able to track how much money comes in and out.
Statistics
- Overall employment of woodworkers is projected to grow 8 percent from 2020 to 2030, about as fast as the average for all occupations. (bls.gov)
- The U.S. Bureau of Labor Statistics (BLS) estimates that the number of jobs for woodworkers will decline by 4% between 2019 and 2029. (indeed.com)
- Woodworkers on the lower end of that spectrum, the bottom 10% to be exact, make roughly $24,000 a year, while the top 10% makes $108,000. (zippia.com)
- In 2014, there were just over 237,000 jobs for all woodworkers, with other wood product manufacturing employing 23 percent; wood kitchen cabinets and countertop manufacturing employing 21 percent. (theartcareerproject.com)
External Links
How To
How to make wood joints
This tutorial will demonstrate how to join two pieces together of wood. We'll use the "pocket hole joint," which means we drill holes in the wood and then glue them together. If your wood is straight and flat, this method will work well. Try dowel joinery instead if your wood doesn't look straight. Here are the steps
-
Drill Pocket Hole Joints. First, measure the area where you wish to place the pocket joint. With a handheld drill machine or jig saw, drill 3/4-inch deep holes in the ends of each piece.
-
Sand Smooth. Sanding the wood's edges will help ensure that the joint won't split later.
-
Glue together. Apply glue to both the ends of the wood. Allow it to sit for approximately 5 minutes before you clamp the pieces together.
-
Attach the Pieces together. After the glue has dried properly, clamp the pieces together to make sure they are flush.
-
Trim Joinery. Trimming the joinery after glue has completely dried.
Be sure to leave enough space between each piece so that they can be turned inside-out.